Heating Systems
An energy efficient home by definition has very little heat loss because of high insulation levels and airtight construction. This leads to two problems: finding a properly-sized heat source and providing adequate ventilation to maintain indoor air quality.
Except for extremely cold periods, a properly designed and constructed energy efficient home can sometimes gain almost enough daily heat from 'waste' sources such as the heat given off by lights, people and appliances. During sunny, cold days solar energy gains also contribute to reducing the heating load. These heat sources are often called 'internal gains'.
Modern control systems such as programmable thermostats can further help to reduce heating energy consumption.
Sizing the Heating System
Heating equipment in a home must be capable of maintaining an interior temperature of 68 to 72° F (20 to 22°) during the heating season. Heating equipment is generally oversized for most homes, but is even worse if the home is an energy efficient home. This leads to frequent on/off operation reducing both efficiency of fuel use and service life of heating equipment.
A heat loss calculation is required to determine the heating system required. It should have a capacity of no more than 10% in excess of the calculated requirement. Installing the smallest capacity heating equipment to meet the loads will save both energy and money. Calculation of total home heat loss is generally done by heating contractors. Contractors inexperienced in understanding low energy house design and heat loss, however, may still result in drastic over sizing. A simple heat loss calculation method is provided in this section.
Isolating The Heating System
If a fuel burning furnace, boiler and/or hot water heater is required, building an airtight enclosure (mechanical room) around the appliances can help control chimney heat loss. Separate combustion and fresh air supplies feed into this room. No previously heated air is used by the fuel burning appliances and cold outside air is prevented from entering other areas of the home. This isolated room must be insulated and sealed from the rest of the home. Water pipes and heat supply ducts should also be insulated.
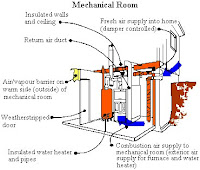
Calculating Heat Loss
Calculating the heat loss from a home is quite simple. The heating requirement will be highest when the outside temperature is lowest and there is no solar gain. A cold winter night is when the heating load will be greatest. Heat flows out through all the building surfaces including walls, ceilings, floors, windows and doors.
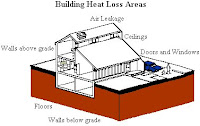
Heat loss through each surface can be calculated using the following equation:
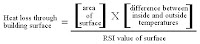
Heat is also lost through infiltration and exfiltration - air leakage. This heat loss can be calculated using:

Note: change the constant 0.36 to 0.018 Imperial units.
There are also a number of sources of heat gain in a typical house. Not only do the occupants give off heat, appliances and lights contribute significantly to home heating. Each person can provide about 75 watts of heating energy while 200 or 300 watts are available from appliances (like freezers, ranges, refrigerators, etc). The average home therefore provides 500 or more watts daily of the total energy required for space heating.
An example heat loss calculation is shown using Plan 13 from Energy Efficient House Plans post. Plan 13 is a 1,920 square foot (178 sq. metres) two level, rectangular bungalow. If this house was to be built in the Red Deer (Alberta, Canada) area, the outside heating design day temperature is - 26° F (-33° C). A common inside temperature is 68° F (20° C) - the difference between them is 94° F (53° C). Design day temperatures and heating degree days information for your locale is usually available from your local weather office. A short list is provided as an example of January design temperatures and degree days for various Canadian cities.
The first set of equations is used to calculate the heat loss from each of the seven surfaces (substitute the areas, R-values and the temperature difference for each surface from your plan). The air leakage heat loss is next calculated using the second equation. The building air volume is 16,775 cubic feet (475 cubic metres) and an air change rate of one-third (1/3 of the house air is replaced every hour with fresh air) can be used in the equation (a typical rate for a well-built, energy efficient home). Substitute the house volume from your plan into the equation. Using the same temperature difference, the total air leakage heat loss is calculated and added to the surface heat loss figures. Subtracting the heat gain average of 500 W results in a total space heat requirement of 8200 W for this example (8.2 kW or about 28,000 btu/hr).
There are a wide variety of computer software programs available which can be used to more accurately calculate building heat loss. These programs require a detailed breakdown of each building component and complete area weather data. Most of the programs available require a considerable learning curve and are often not practical unless you do a lot of heat loss calculations, are a house designer or are designing a complex solar building.
The efficiency of the heat source must be taken into account when selecting it. In the example, an 8.2 kW heat source would be needed (28,000 btu/hr). If one chooses a 100% efficient electric heating source, the exact figure calculated above can be used to size equipment. Gas furnaces range from 70% to 80% efficient (measured seasonally - over an entire year of operation). Divide the heat load (8.2kW) by the system efficiency (0.70) to obtain the 'bonnet' size of 11.7kW (40,000 btu/hr) necessary to provide 8.2kW. Gas-fired furnace and boiler units with efficiencies of 90% to 95% are also available but are usually produced in large output sizes and are more expensive.
Heating Systems - Forced Air
Forced Air Distribution Systems
Homes incorporating forced-air heating systems are very efficient at distributing heat around a home, preventing stagnation of air and moving heat from different sources to the overall space. They also work well with mechanical ventilation systems. The central heat source could be a fuel-fired furnace. Unfortunately the smallest sizes usually available are in the 50 to 60,000 Btu/hr range (18 kW ) and this heating capacity is often much too large for an energy-efficient home. Using such a large heat source is inefficient in terms of fuel consumption. For example, a 50% oversized furnace will use 20% more fuel in heating the same space than a correctly sized unit.

Good heat distribution, air movement, filtering capability, humidity control and low maintenance are some of the advantages with a properly designed and installed forced-air heating system.
A forced-air distribution system works well if a home receives abundant solar energy. Since passively heated spaces can easily overheat when the window area is too large or if there is not enough mass to absorb and store the solar energy, having continuously circulating air with the forced-air distribution fan running at a slow speed helps prevent overheating. Passively heated air is distributed to all the spaces in the home, not just those on the south side.
High Efficiency Gas Furnace
High efficiency (condensing) forced-air gas furnaces offer efficiencies of 90% or better. These units use electronic ignition, induced draft fans and condensing heat exchangers. Ductwork and installation is similar to a standard furnace with the exception of the chimney and condensate drain. Condensing furnaces require a drain pipe connected to a floor drain to allow condensation (water) from the heat exchanger to drain. A standard chimney is not required because the exhaust air temperature is reduced to the point that high temp plastic pipe can be used as an exhaust vent out of a side wall.
The diagram shows a fresh air duct from outside, ducted directly into the cold air return. Combustion air is separately ducted from the exterior to the front of the furnace. Note that both air ducts are insulated. Although not shown, an air to air heat exchanger should be installed to maintain indoor air quality.

Radiator (Fan Coil Unit)
A good heating solution for an energy-efficient house is to use the advantages of a forced air system (such as good air and heat distribution, filtering capability, low maintenance) and add a small auxiliary heat source to it. This could be an electric heating element, a hot water heated coil unit, a heat pump or simply a separate wood or electric unit providing heat that the system picks up and distributes via the forced air system.
This example shows how hot water heating can be combined with a forced air system. Hot water from a boiler is circulated through a radiator placed in the ducting of a forced air system. A fan forces the air through the radiator where the heat is picked up and distributed to the entire house. The duct work design is the same as any forced air system.
An air to air heat exchanger helps to maintain indoor air quality by suppling pre-heated fresh air to the cold air return, which is then distributed to the rest of the house by the forced air system.

Heating Systems - Hydonic Systems
Hydronic Heating Systems
Hot water (hydronic) heating systems usually consists of a boiler and a heat distribution system. This distribution system shows baseboard radiators. A wide variety of radiator types are available. Hot water is supplied directly to the radiators and returns to the boiler by way of a separate line. An expansion tank provides a cushion of air for heated water to expand into if pressure builds up in the system. An insulated fresh air duct provides combustion air directly to the boiler.
Because hydronic systems have no air movement an air to air heat exchanger is used to maintain indoor air quality and transfer heat from the exhaust air to the incoming fresh air supply. Fresh air is supplied (individual ducts) to each room while exhaust air is removed from the kitchen, bathrooms, hallways and laundry rooms. Two separate ducts (intake and exhaust) are installed through the floor header area and must be at least 12 feet (4 m) apart to prevent cross-contamination.
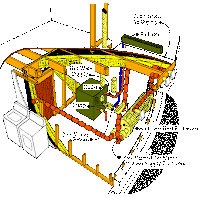
Radiant Floor Heating Systems
Radiant floor hot water heating systems work well in an energy efficient home. Hot water is distributed through water pipes installed in the floor. The layout and distribution of pipes is determined by the building heating requirements. Insulation is necessary under basement floors to help reduce heat loss to the surrounding earth. A reflective material and Insulation are recommended for all floors to maintain heat transfer in the desired direction (usually upward).
With this type of heating system, a balanced mechanical ventilation system which exhausts stale air and supplies fresh air separately (preferably to every room) is essential to maintain indoor air quality. Air to air heat exchangers (also called 'Heat Recovery Ventilators') are recommended for energy efficient homes.

Heating Systems - Other Systems
Electric Systems
Since chimneys are a source of air leakage, electrical heating systems have merit in that no chimney is required. Although electricity is a higher priced fuel, its increased efficiency and minimal capital cost combined with the small required output in an energy efficient home make it a potential alternative.
This system uses an electric heating element placed in a forced air system This combines the benefits of forced air and a small heating system to match the heating load of an energy efficient house. There are also a number of radiant electric (ceiling or floor) panel systems available for home heating.
Fresh air from the heat exchanger is distributed throughout the house by the forced air system.

Heat Pumps
Heat pumps transfer heat by circulating a refrigerant (gas) through an evaporation- condensation cycle, similar to a refrigerator. Winter heating and summer cooling are both handled by a single system. Heat pumps can operate using water, ground or air as the heat source. These systems use electricity to extract heat and under normal operating conditions will produce at least three times more heat energy (or cooling) than they use in electrical energy.
This diagram shows an air to air heat pump system with forced air delivery. During the winter cycle, heat is extracted from the outside air and released into the house. In summer, heat is extracted from air inside the house and dumped outside, thereby cooling the house. One potential problem with air base heat pump systems is that they use more energy than they produce if outside air temperatures drop below 50° (10°).

Combined Systems
Combined systems are now being offered which provide both space heating and domestic hot water. Systems are available which use fossil fuels, heat pumps or electric resistance heating sources to provide domestic hot water and space heating from one unit. Available with smaller output ranges these units should work well with an energy efficient home.